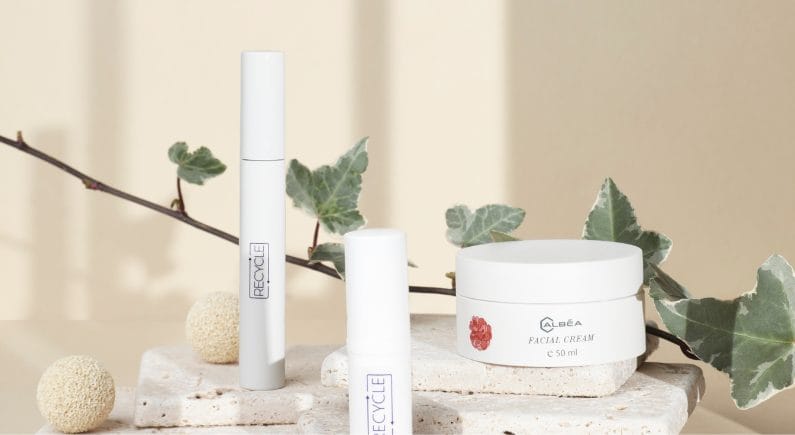
Key learning about recycling make-up or how Albéa developed RECYCMakeUp in partnership with CITEO
Why RECYC MakeUp?
In an era marked by increasing regulatory measures, legislative initiatives such as the AGEC (France), Climate and Resilience Act (France), PPWR (Europe), and California SB54 (USA) have propelled the agenda towards sustainable packaging practices. These regulations emphasise recyclability, reusability, reduction, and the integration of recycled materials, while also imposing bans on certain packaging materials like styrenic polymers.
By enforcing deadlines for compliance, such as the January 1st, 2025 ban on specified packaging materials (in France), these laws are reshaping industry standards. Moreover, with mandates for incorporating post-consumer recycled content and restrictions on the use of "compostable" plastics, the landscape of packaging design faces significant transformations.
The urgency for change is evidenced by the stark reality that the majority of make-up and skincare packaging remains non-recycled and ill-suited for recycling.
Albea answered the projects' call from CITEO for recyclability insights in order to collectively push towards establishing clear roadmaps for achieving recyclability objectives. It resulted in a collaborative R&D project that was named RECYMakeUp.
Understanding Recycling Requirements
Beauty packaging and especially make-up is often highly complex: small, compact (heavy), cylindrical, multi-material, using plastics with no existing recycling stream in packaging (such as ABS), and highly decorated.
The project RECYMakeUp aims to develop prototypes of PP and PET packaging prototypes in PP and PET, to move away from plastics with no-recycling streams in packaging (such as ABS). Then, it will study the sorting and recycling behaviour of these new PP and PET made packaging materials and identify the challenges and opportunities associated with the substitution of certain materials for the cosmetics industry. Finally, it will contribute to the definition of This will in the end, help define "Design-for-Recycling Guidelines” specific to those small packaging.
Two phases of analysis
RECYMakeUp is focusing on 2 stages of the recycling process: sorting and regeneration. Usually, the recycling process comprises four phases from collection to sorting, regeneration and recycled materials as result.
Results and learnings
The first learnings concerning the sorting stage are related to materials and decorations:
- PP (polypropylene) seems highly detectable.
- HDPE (high density polypropylene), PP or PET (polyethylene terephthalate) need to be detected with a high rate.
Decorations
- Decoration such as partial metallisation (or hot stamping) does not impair the material detection phase. Fully metallised packaging is not detectable.
- Mass colours (Masterbatch) and "light" inks allow for perfect detection of materials while carbon blacks prevent readability and should be avoided, and only blacks that are approved by Cotrep can be accepted in the sorting stream in France.
- Ultra-transparent packaging seems very difficult to detect and be recycled
Shapes
- Non-compressible "rolling" packaging is very difficult to identify and sort at eject at the sorting centre since they would roll on the conveyor belt. They tend to move positions between detection and ejection. If the packaging is not ejected, it cannot be "sorted" and therefore cannot be recycled.
More on this on Recycling report on re/sources:
Materials
- Some combinations of materials do not interfere with regeneration/recycling, while others will., as they can be separated by density flotation:
- ABS, PS, Polyesters are acceptable in the PP (polypropylene) and HDPE (high density polypropylene) streams
- PE (polyethylene), and PP are acceptable in the PET (polyethylene terephthalate) stream
- PE will impair the PP stream
- Metals, glass, ABS, PS, PBT, etc. will degrade in the PET stream
Substitution of complex or problematic plastics
The first learnings from the substitution of ABS and SAN for PP et PE for instance.
ABS and SAN do not and will not have a recycling stream for household packaging. They must therefore be replaced in large part by plastics that have or will have a recycling stream for packaging:
- PE, PP, PS, PET bottle
- Certain CoPET in the future
ABS and SAN have no equivalent in PP or PET/CoPET so compromises will have to be made in terms of performance. Polyesters are by nature semi-crystalline materials, unlike ABS which is by nature amorphous. They are much more complex to inject and mould (injection point, cooling, specific moulds). Some parts will have to be redesigned and decorations (chemistry and process) will have to be adapted since polyesters are sensitive to high temperatures.
Key Takeaways
The design of packaging needs to be (re)developed or reinvented to improve the success rate in sorting different types of packaging (rolling, small and heavy, highly decorated, etc.).
At the same time, it is important to encourage avenues of development using “recyclable” resins
Recycling streams are being developed and will help us meet THE targets.Albéa Cosmetics & Fragrance begun to incorporate these design principles into their new ranges of "We are ready for 2030" packaging (below).
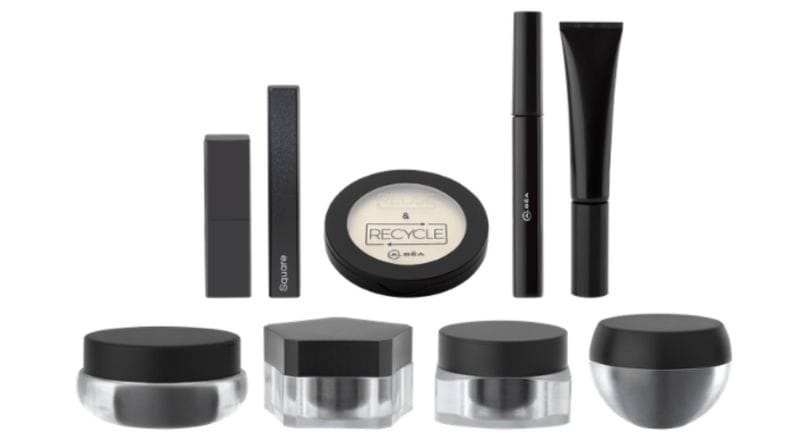
Lexicon
- PE - PolyEthylene or polythene - most commonly produced plastic primarily used for packaging.
- PET - PolyEthylene Terephthalate - most used plastic in the world, in textiles, transparent drink bottles or food containers for instance.
- PP - PolyPropylene - hard and resistant matter that is mostly used in caps and hard packaging pieces.
- L / HDPE - Low or High-Density PolyPropylene - used in personal care squeezable bottles, for instance, used for tensile strength and moisture barrier.
- ABS - Acrylonitrile Butadiene Styrene - opaque thermoplastic, mostly used in hard pieces like make-up packaging.
- SAN - Styrene Acrylonitrile resin (commonly referred to as Acrylic) - rigid, transparent (glass-like), tough, resistant to greases, stress cracking and crazing, easily processed and resistant to greasy stains. SAN is used in transparent cosmetics jars or bottles with a glass-like effect.
Sources: 7 different types of plastics, ABS, PE, SAN, PP.